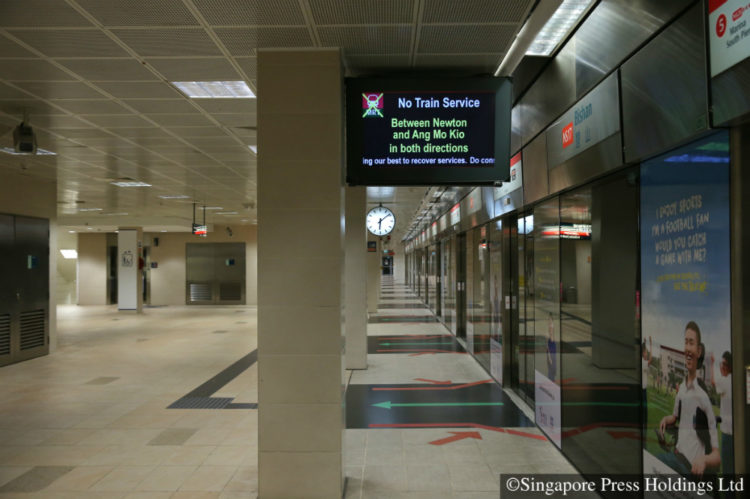
MRT service was still down at 6am on Sunday morning (Oct 8) between Ang Mo Kio and Newton, after flooded tunnels caused disruption on the North-South Line on Oct 7.
Like in rail transportation, enforcing maintenance regimes plays a critical role in sectors such as aviation, public bus service and chemical engineering.
While staff may cut corners, having experienced quality audit teams, a maintenance structure and a strong safety culture can help in spotting problems before they result in widespread failure, experts in those fields told The Straits Times yesterday.
On Tuesday, SMRT revealed that staff in charge of the pump system of a storm water pit had signed off on maintenance work that was not done. This led to flooding of the train tunnel at Bishan station last month, rendering services on a stretch of the North-South Line inoperable for 20 hours over two days.
It is suspected that the falsification of the quarterly records went as far back as December last year.
SMRT said on Tuesday that it will engage external experts to carry out a system-wide inspection, and form a 50-strong inspection team that reports independently to its Board of Audit and Risk Committee.
Asked about the latest revelations, an engineer from the public bus sector, who declined to be named, said: “What surprised me was that the team got away with it for so long.”
He said a quality audit team conducting random spot checks would keep staff on their toes. But being able to spot anomalies – such as signs that parts have not been removed or dismantled for servicing, or paperwork being too neat and clean – comes with knowledge and experience, he added.
Discrepancies can also be flagged by other departments like storekeeping, such as when spare parts that are ordered and scheduled to be used accumulate on shelves – a sign that maintenance work has not been done, he said.
But lapses can still fall through the cracks. He said: “If the guys are signing out the (replacement) parts and throwing them away, it gets difficult to catch.”
In the chemical and process engineering field, a highly structured method of managing maintenance is employed.
This is by using an international asset management standard, to classify all plant equipment – such as pumps, motors, valves and compressors – into a risk matrix in terms of failure frequency and consequence, said Mr Norman Lee, chairman of the chemical and process engineering technical committee with The Institution of Engineers, Singapore (IES).
Different maintenance efforts are applied, based on where each piece of equipment falls in the matrix. “For example, if (the) failure of a pump can cause the complete loss of production, it has a high failure consequence, and maintenance efforts will include predictive measures like regular monitoring of bearing temperatures and vibration readings,” he said.
If not already adopted, having similar maintenance methodologies in SMRT would serve as a “good yardstick”, Mr Lee said.
Following the flooding incident, SMRT said last month that it will improve the redundancy of flood prevention measures, including additional radar sensors to activate pumps, on top of float switches.
In aviation, a strict regime of regular preventive maintenance – based on aircraft manufacturer requirements – is followed by internal and external audits, said Mr Abbas Ismail, course manager for the diploma in aviation management and services programme at Temasek Polytechnic.
While audits are “bound to turn up” minor procedural lapses, caused by factors such as fatigue or carelessness, he said they are important to ensure that major lapses do not happen.
Mr Lim Yeow Khee, a member of the IES’ aerospace advisory committee, said the Civil Aviation Authority of Singapore certifies aircraft maintenance companies, and critical processes also require duplicate inspection.
There has also been a focus on fostering a safety culture, with a strong effort to encourage reporting of errors and violations in the workplace, he added.
• Additional reporting by Zhaki Abdullah
Related story: Transport Minister says flooding in tunnels was preventable
Related story: Experts say more measures needed to prevent flooding in tunnels