
Air suspension components of a Mercedes-Benz E-Class.
Cars with air suspension use air as the springing element instead of steel coils, torsion bars or leaf springs. The function of the spring in any vehicle is to maintain its ride height while allowing vertical motion of the wheel over undulations.
To this end, the springs absorb shock from surface irregularities. What people commonly call the “shock absorber” is a damper and its sole purpose is to attenuate the natural bouncing motion of a spring.
Indeed, a damper does not absorb shock, but is a critical component of any spring-laden suspension system.
In an air suspension, pressurised bellows made of rubber are located between the body and suspension in place of the steel springs. Given a fixed mass of air in a bellow, any change in its volume will cause an inverse change in the internal air pressure.
In other words, squeezing the bellow to reduce its volume will increase the pressure inside. This results in a force that resists compression.
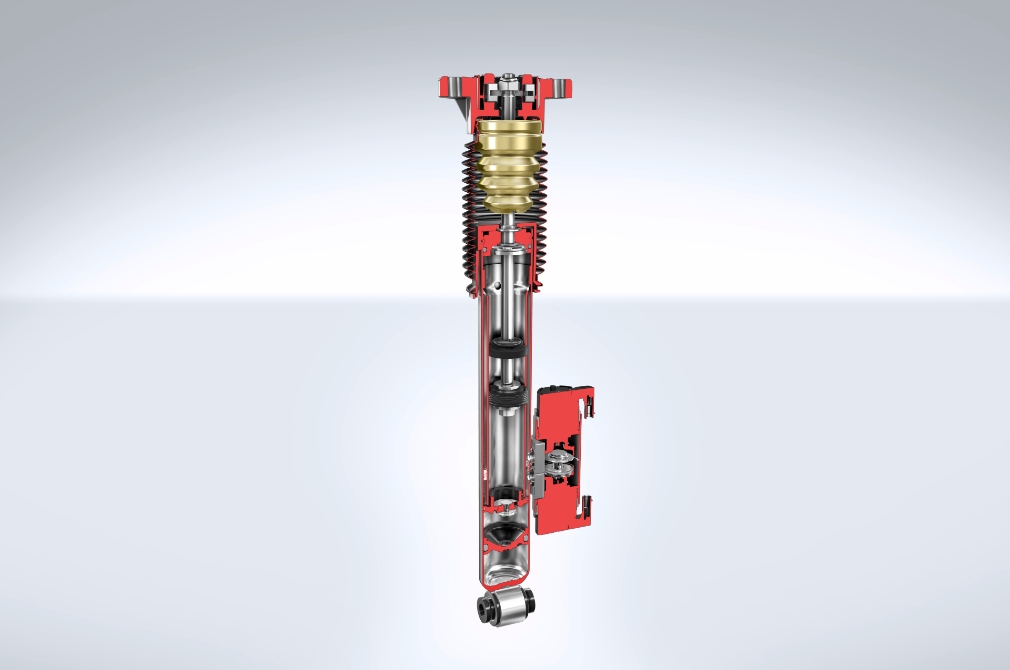
A multi-chamber air suspension strut of a 2015 Mercedes-Benz GLC.
Similarly, an increase in bellow volume causes a drop in pressure. The air-filled bellow thus functions exactly as a spring, enforcing a vertical equilibrium.
With a flexible bellow, an air suspension system provides possibilities to incorporate variable spring rates and adjustability in ride height. Most therefore include an air pump and a valve network for this purpose.
Together with current electronic control technology, air suspensions are capable of achieving an optimal mix of ride comfort, handling stability and customisable ride height.
They cost more than conventional steel springs, and hence are commonly found only in higher-end cars. But they are also used in many trucks and buses.
When you consider that an entire vehicle sits on rubber tyres filled with air, it will come as no surprise that a pressurised rubber plenum is capable of suspending a vehicle.
Feeling technical? Click here to learn more about air suspensions in greater detail