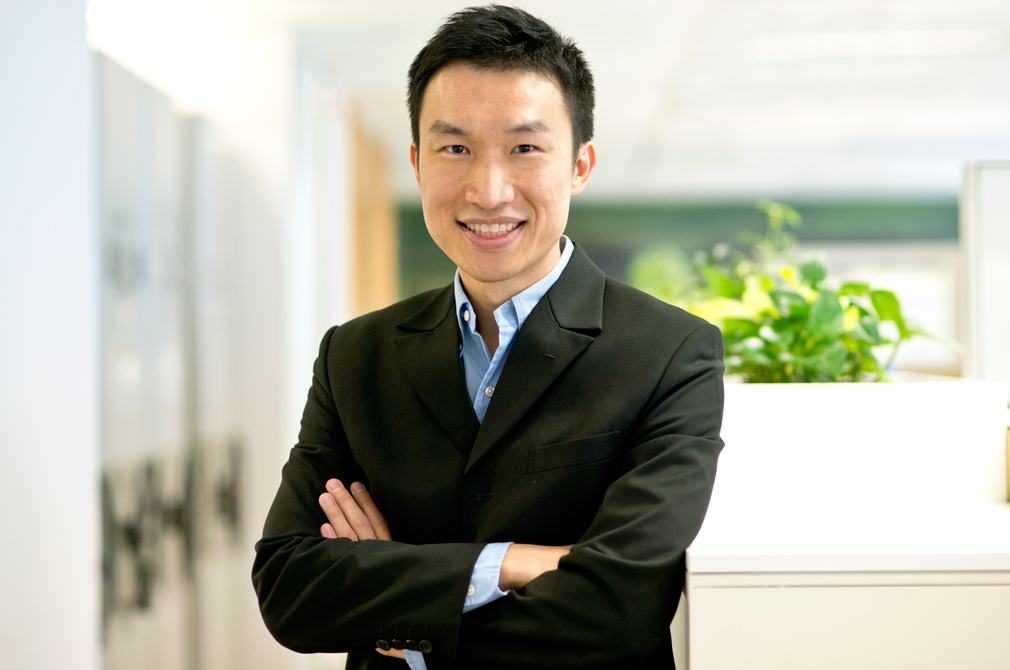
Lennard Kwek, Head of Marketing, Bridgestone Asia Pacific.
Today, carmakers and consumers alike prefer larger wheels, which means bigger tyres. The problem with this is that larger wheels are not very environmentally friendly. And today, when sustainability is a buzzword in every industry, this presents a conundrum.
Can tyre firms become more sustainable while still delivering high-performance products?
To find out more about these issues, Torque spoke to Lennard Kwek, Head of Marketing of Bridgestone Asia Pacific Pte Ltd.
Lennard shares with us how Bridgestone is adapting to these requirements, and tells us how it is meeting the challenge of making tyres for electric vehicles (EVs).
Carmakers are fitting larger wheels to their vehicles. However, these have more rolling resistance and lower efficiency. How do you balance this, given the need for lower emissions?
Larger diameter tyres have been gaining popularity as consumers recognise their aesthetic appeal and greater performance. These include greater stability, improved grip and shorter braking distances, especially in wet conditions.
Rolling resistance is one of the key speed bumps to achieving high fuel – or battery – efficiency in vehicles. To that end, our ENLITEN technology enables super low rolling resistance in our tyres and reduces the raw material requirement in their production.
ENLITEN technology tyres demonstrate up to 30 percent less rolling resistance than a standard premium summer tyre, and up to 2kg less raw material used for each tyre.
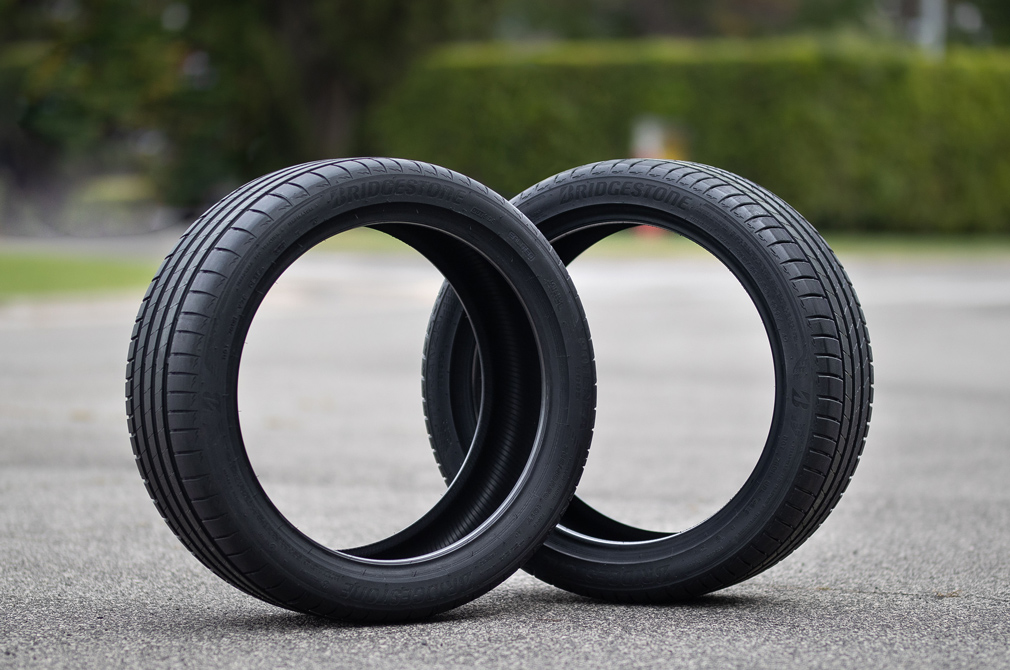
Bridgestone’s tyres with ENLITEN technology.
Last year, we partnered with Volkswagen to equip its first all-electric ID.3 vehicle with our ENLITEN-enabled Turanza Eco tyres.
On a molecular level, we leverage on our NanoPro-Tech (Nanostructure-Oriented Properties Control Technology), that helps us achieve market requirements in rolling resistance, wear, wet and dry performance in a wide range of tyres.
Larger tyre sizes cost more to produce. But with the increased demand and production of them, will tyre manufacturers end up having better economies of scale?
The increased demand and production of large tyre sizes should result in better economies of scale for manufacturers, but it is a bit more complex than that.
Other factors like the wider range of unique sizes, as well as increased raw material requirements and transportation cost do cut into the cost-savings from large-scale production.
Because of the wide range of unique sizes, which is especially fragmented in mature markets, manufacturers must balance between size selection and vehicle OEM requirements, which can differ greatly from market to market.
To tackle the larger range of unique sizes for large size tyres, we continually focused on improving production efficiency by making use of modular designs, which allow us to simplify the design and production process.
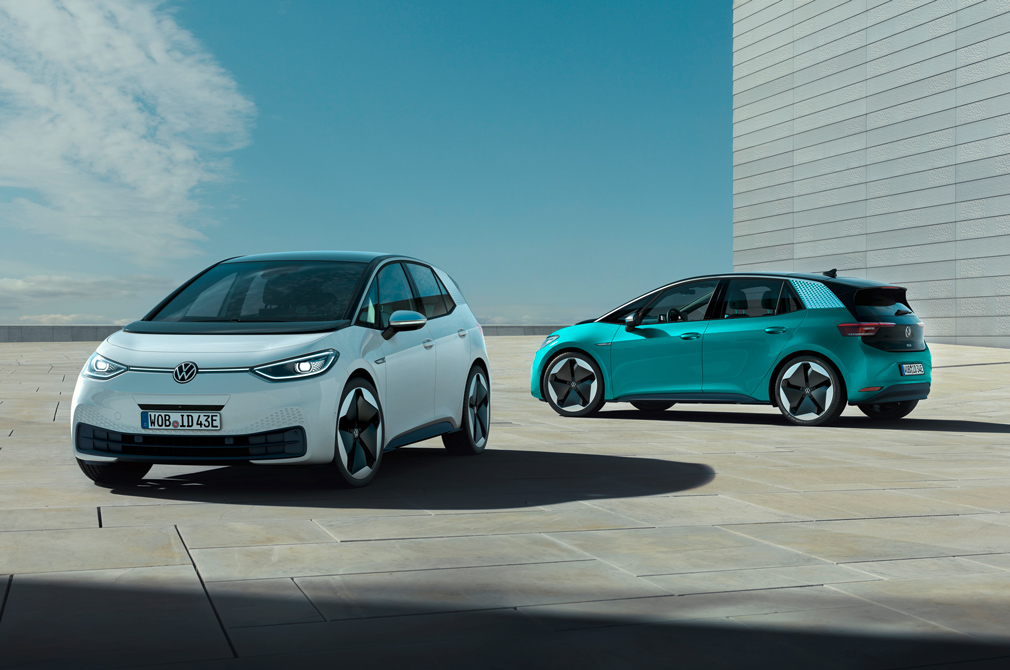
Volkswagen ID.3.
To minimise transportation cost, we have managed tyre size allocation optimally within our Asia Pacific plants, which allows for reduced time taken for distribution to market as compared to importing from Japan or Europe.
Our production is typically based on market tyre demand. With larger demand, there will be a corresponding increase in production which will lead to natural economies of scale.
Having a balance of our size selection with production and vehicle OEM requirements also help us to drive efficiency in production through the use of modular designs.
Do you see the segment for smaller tyre sizes (e.g. 15-17 inches) growing smaller?
Based on our own market research in the Asia Pacific market, we are seeing a rising proportion of larger-rim tyres, so the segment for smaller tyre sizes has been decreasing over the years accordingly.
This has been supported by the rising share of SUVs and crossovers in the markets. However, in specific markets like Indonesia, smaller tyres still retain a larger proportion.
Which segment is seeing more growth – the high-performance segment or the eco-friendly segment?
While we are seeing an increasing focus on sustainable products, there is a challenge in ascertaining the market size for eco-friendly tyres.
Some manufacturers do not have specific eco-friendly tyre products, and instead include “fuel-saving” as a feature for their existing products. So, this somewhat dilutes the eco-friendly range of tyre products, and makes it difficult to separate them from “normal” tyres with fuel-saving features.
There are also more and more vehicle models that have been equipped with eco-style driving options, which enable the vehicles to reap fuel efficiency even while using tyres that are not specifically eco-friendly.
What are some examples of sustainable materials/ingredients that are being used in tyre-making?
We are expanding the use of recycled raw materials, such as recycled rubber and recovered carbon black, to improve the productivity of natural rubber and develop bio-derived raw materials.
In 2020, we announced the development of a highly precise diagnosis technology for disease in Para rubber trees, which makes use of both AI and big data.
In the Americas, we have also partnered with Delta-Energy to use recovered carbon black to manufacture new high-quality tyres for agriculture and passenger vehicles in Des Moines, Aiken County and Cuernavaca.
The key to achieving success in sustainability is to forge partnerships with local manufacturers and raw material producers in every region.
How are tyre brands making the end-of-life/disposal/recycling process for tyres more sustainable?
One efficient way to improve end-of-life and recycling of tyres is through re-treading. By replacing worn tyre treads rather than just disposing of them, we can reduce the raw materials used to less than one-third that of new tyres.
At the same time, we are also cutting the amount of scrap tyres as other components of the tyres can be reutilised.
Bridgestone has developed durable tyre carcass that prevents unpredictable wear and enables more manageable maintenance.
This allows for the tyres to be re-treaded several times. By doing so, we can fully maximise each tyre’s life, which helps cut CO2 emissions.
EVs produce a lot of instant torque, which potentially means greater tyre wear. Is a hardier or more wear-resistant tyre more cost effective and sustainable to produce?
Yes, a more wear-resistant tyre would ultimately be more cost-effective and sustainable to produce, as it would reduce the frequency of tyre replacement and cut the raw material requirements to equip a vehicle for an extended period of time.
The tyre requirements for EVs are significantly different from fuel-based vehicles, and we have had to rethink tyre development and design from the ground up.
We see EVs as the future of mobility, so it is important that all aspects are designed and produced with sustainability and efficiency in mind.
Do you see tyres becoming part of this connected eco-system, so that they can also display information such as wear rates and rolling resistance?
Leveraging on technology is the way forward to advance the proliferation of EVs while maintaining safety and performance standards.
We have designed our own proprietary sensor technologies – Contact Area Information Sensing (CAIS) and Smart Strain Sensor (SSS). Both CAIS and SSS make use of sensors that are attached to the inside of tyres to monitor their condition during driving.
CAIS is able to estimate tyre wear and measure tread depth and inflation pressure of the tyre, while SSS is able to estimate wheel axle load tyre condition, inflation pressure and temperature of the tyre.
Both technologies will be instrumental in enabling end-users to identify the most appropriate timing for tyre replacement, and also predict maintenance issues and improve overall safety and productivity for vehicle fleets.
The key differentiators for SSS from other similar sensors available in the market are its longer battery lifespan and independence from speed, which means it can make reliable measurements even at low speeds.
5 things you can do to help tyres last longer
Is grip down to tyres alone? Find out here!
Why do high-performance tyres make your ride bumpy?