Our mechanical engineer talks about the nuts and volts of battery-powered automobiles in the first of a two-part article.
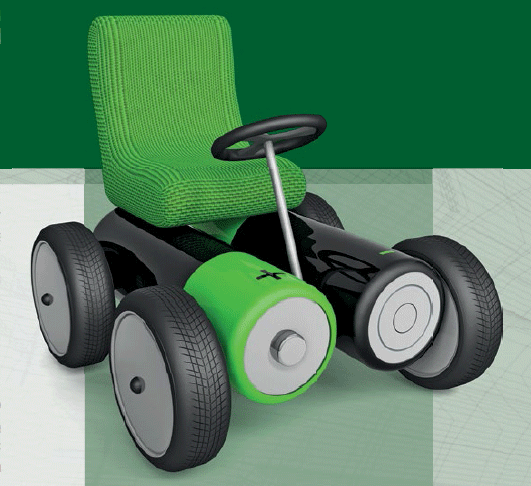
THE 21st century electric car is still constrained by a number of practical issues, which include charging time (the single biggest drawback), driving range on a full charge and kerb weight.
Even with state-of-the-art Ni-MH (nickel-metal hydride) and Li-ion (lithium-ion) batteries, most electric cars today can barely reach 200km on a complete charge/recharge, which takes between two and eight hours.
The good news, though, is that almost all major automobile manufacturers and their relevant partners/suppliers are charged up about battery technology, so we’re likely to witness big breakthroughs in electric vehicle propulsion during our lifetime.
The biggest breakthrough needed is 100 percent charge in less than 10 minutes, along with a realistic (rather than optimistic) range of at least 400km.
An electric car generates its juice differently from a traditional car with an internal combustion engine. The latter converts chemical energy, which is fuel in the form of petrol or diesel, into heat energy (combustion), and then into mechanical energy.
With an electric car, there’s an intermediate stage where the energy from the battery/batteries is converted to electricity, which drives an electric motor that provides the traction effort thereafter.
A hybrid drivetrain couples an electric motor to an internal combustion engine, with the two components transmitting power to the driven wheels either independently or in unison.
Strictly speaking, an electrically driven car with a petrol or diesel engine that serves purely as an electricity generator is not a hybrid.
Hence, the Toyota Prius and BMW i8 are hybrids, but the BMW i3 is not. The i3’s little 2-cylinder engine in the boot merely charges the batteries and isn’t mechanically linked to any of the wheels, so it plays no role in the tractive force of the hatchback.
Now, let us take a look at the pure electric car. Essentially, its electrical powertrain consists of a battery pack, a power controller, one or more electric motors, and the transmission set. The suspension system is similar to that of any modern motorcar.
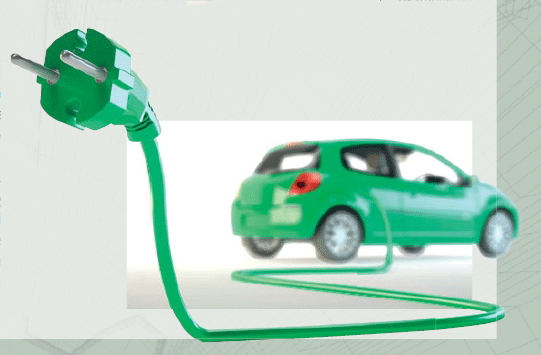
Since the batteries function as the on-board energy store, they must have the capability to be refilled with energy. Therefore, all batteries used in electric cars are of the rechargeable type – even the lead-acid cells used in the very first electric cars of the early 1900s.
With the benefit of a long development history, the leadacid battery is still used for vehicles such as golf buggies, forklift trucks and certain airport runabouts. These batteries are robust and relatively inexpensive, but their very low energy density (capacity per unit weight) and slow recharging make them unsuitable for use in passenger cars.
For this reason alone, the current preferred type of battery for electric cars is lithium-ion, which has roughly six times the energy density of lead-acid.
The same comparison with petrol reveals an energy density more than 60 times higher than lithium-ion batteries! This, in fact, was the original reason why the petrol-fuelled “horseless carriage” made the nascent electric car obsolete back in the 1920s.